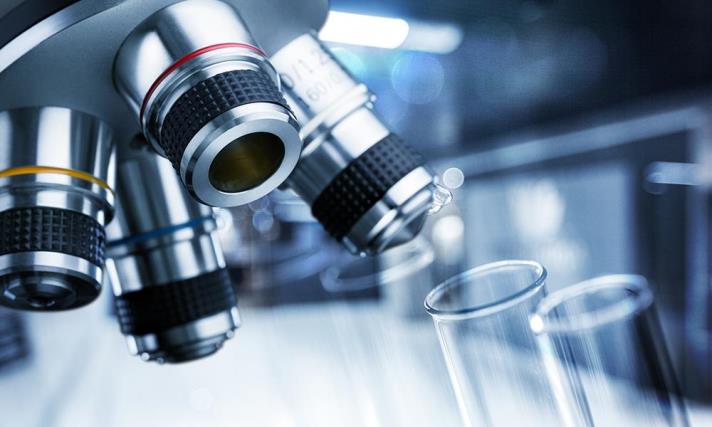
The challenges for primary packaging and delivery systems
By Rich Quelch, Global Head of Marketing, Origin
GSK, Bristol-Myers Squibb, Novartis and AstraZeneca to name but a few are investing billions of dollars in biologics to have prime mover advantage in a market forecast to be worth nearly $480 billion by 2024.
That being said, biologics aren’t exactly new; evidence exists the Chinese first developed smallpox inoculations as early as 1000 CE. Fast forward to today and the science has become dramatically more sophisticated; efforts are even underway to manufacture biopharmaceutical proteins in plants.
This all sounds extremely promising, but the rapid rise of biologics has thrown up huge challenges for packaging to deliver safe and effective products. If these aren’t overcome, we risk halting progress on these groundbreaking new treatments and ultimately, put health outcomes at risk.
Eliminating contaminants
Therapeutic proteins are very different from traditional small-molecule medicines. Essentially, biologics are ‘nano-machines’ whose functionality depends on their molecular shape and delicate structure.
Degradation during transport, storage and usage is a large concern. Proteins are very sensitive to metal ions, so a crucial issue that must be taken into account is the accumulation of ‘
The current reliance on polyethylenes, polypropylenes and polycarbonates in pharma packaging will mean stakeholders will fail to meet the future efficacy requirements for safe and effective biologic products.
Enter fluoropolymers which, due to the elimination of injection
As a less brittle, lighter and more flexible alternative to glass, cyclic olefin plastics are also growing in popularity because, like fluoropolymers, they’re intrinsically very inert, composed of just carbon and hydrogen. Almost all are very rigid thermoplastics which can be
These next-generation packaging materials, amongst others, are helping to deliver the next generation of medicines.
Optimal delivery systems
By their nature, biologics are difficult to form into solids or capsules, meaning injection is the most common method of delivery. It’s then, no wonder, the global prefilled syringes market is estimated to be worth $22.5 billion by 2025.
A prefilled syringe is a win-win solution for patients, health professionals and manufacturers as it promotes self-administration, reduces overfill waste and lessens the risk of misuse.
However, while silicon oil, used as a lubricant to help move the plunger in prefilled syringes, are considered non-toxic and biocompatible, there’s evidence from microflow imaging (MFI) that protein aggregation can occur. Therefore, each new compound and packaging solution should be tested for individual compatibility and assessed through different temperature, transportation and time scenarios.
As there are limitations on how rapidly any volume of drug can be injected subcutaneously, there’s also a growing interest in wearable injectors ‘ or on-body delivery devices ‘ to improve biologics’ bioavailability and patient experience.
The most advance on-body systems are helping to improve compliance, increase ROI and lower health system costs associated with large protein biologics. They’re also more comfortable for patients and moves treatment from the hospital into the home.
Apply QbD principles
In the pharma industry, innovation has always been synonymous with new drug discovery and approval. However, while there’s no arguing against the importance of developing new medicines, the next generation of packaging and delivery systems deserve the same attention.
With innovations in biologics placing increasing and complex demands on the supply chain, packaging and delivery components must be precision engineered to ensure these groundbreaking new treatments are delivered and administered to patients as intended.
Like experienced by conventional pharma, there’s a steep learning curve ahead to build transferable knowledge. As our understanding of the fundamentals of biologic
The underlying principle of QbD is that quality is built into a product from the outset rather than tested during manufacture.
For example, a self-injection system needs to function consistently and reliably for patients using them at home. QbD-designed components can significantly reduce plunger variation, facilitate more efficient manufacturing processes and boost patient confidence. They can also enable larger-size delivery systems and greater dose volumes to encourage accurate self-administration and reduce wastage.
Standing out from the crowd
Rising investment in the biologics sector is shifting the makeup of the pharmaceutical market, increasing its share from just 16 to 25
In their infancy, biologics were considered first-in-class and unbeatable. However, the market is now maturing and biosimilars ‘ which have no clinically meaningful differences ‘ are becoming more popular. Players can expect a fiercely competitive playing field.
Buyers now have
We’re likely to see packaging designs which incorporate smart value-added features to stand out from the crowd. For example, more exclusive deals will be struck to secure access to enhanced delivery devices; vacuum insulated panels added to cut cold chain risks and hibernation capabilities to extend a product’s shelf life if unexpected delays occur.
It’s a testing, yet exciting time, for the pharmaceutical industry. The companies that master the art of delivering biologics in a safe, efficient and convenient way will empower both patients and healthcare professionals with the utmost confidence as they look to treat often life-altering conditions.